The Consequences of China’s Overcapacity
China’s persistent problem of overcapacity in various industries is proving to be a double-edged sword, with far-reaching consequences for both domestic and global markets. In this article, we delve into the reasons behind China’s overcapacity, analyze its impact on industries and economies, and explore the challenges and repercussions it presents for policymakers, businesses, and stakeholders.
Understanding China’s Overcapacity:
China’s overcapacity stems from years of rapid industrial expansion fueled by government-led investment, subsidies, and incentives. In its drive for economic growth and global competitiveness, China has heavily invested in sectors such as steel, aluminum, cement, and solar panels, leading to a glut of production capacity that far exceeds domestic and global demand.
Challenges in Managing Overcapacity:
China’s overcapacity poses numerous challenges for policymakers and industry leaders. Excess production capacity undermines market efficiency, distorts pricing mechanisms, and exacerbates competition, leading to downward pressure on prices, profitability, and investment returns. Moreover, overcapacity fuels concerns about environmental degradation, resource depletion, and energy consumption, as industries struggle to absorb excess output and manage waste.
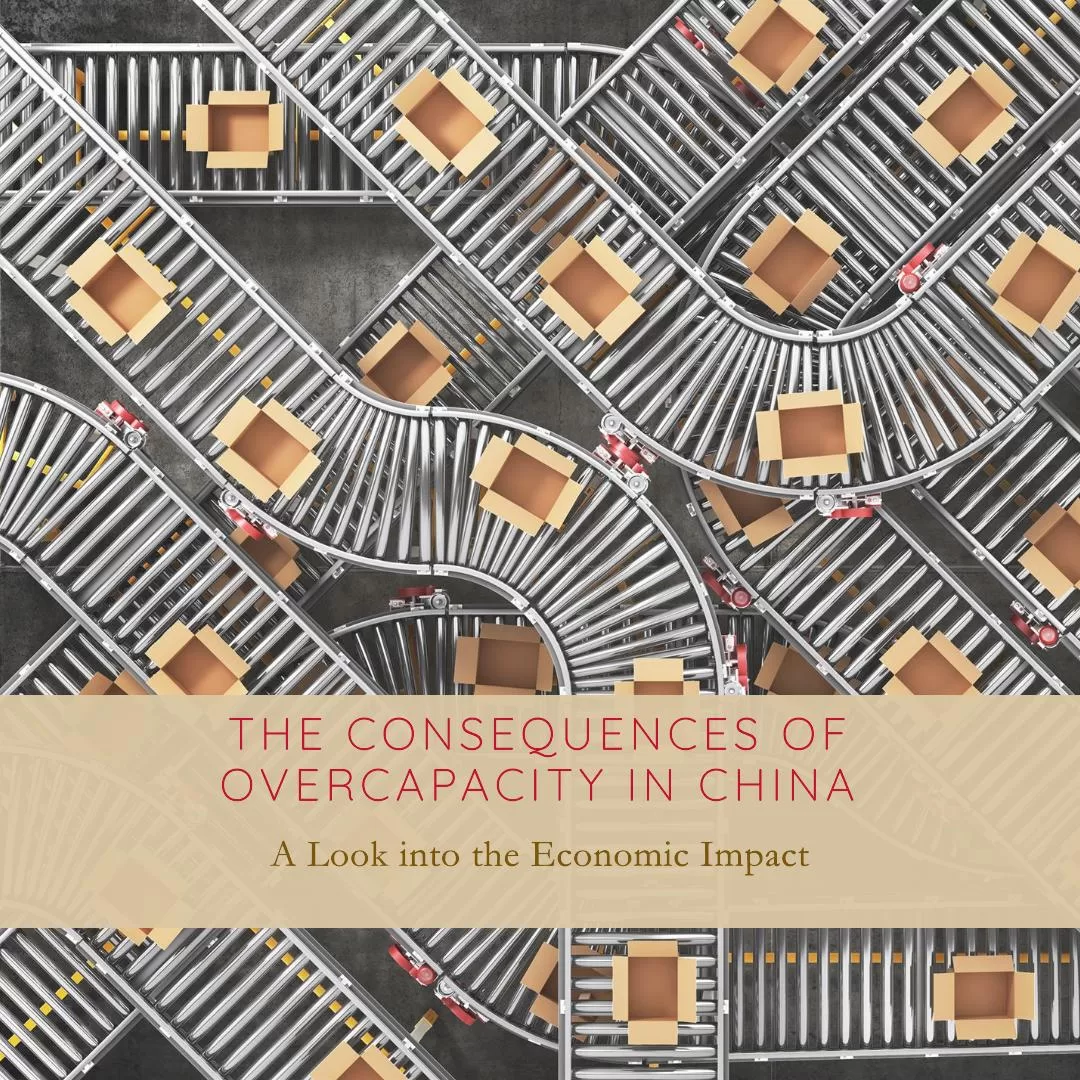
Impact on Global Markets:
The repercussions of China’s overcapacity extend beyond its borders, affecting global markets and trade dynamics. Excess Chinese production floods international markets, driving down prices and undercutting producers in other countries. This phenomenon, often referred to as “dumping,” has sparked trade disputes, anti-dumping measures, and retaliatory actions by trading partners seeking to protect their domestic industries and market share.
Strain on State-Owned Enterprises:
China’s state-owned enterprises (SOEs) bear the brunt of overcapacity, grappling with financial losses, debt burdens, and inefficiencies resulting from excess production. SOEs, often supported by government subsidies and preferential policies, face pressure to maintain employment, social stability, and political legitimacy, even as they grapple with overcapacity and market challenges. Balancing economic imperatives with social and political objectives poses a daunting task for Chinese policymakers and SOE managers.
Shift Towards Quality and Innovation:
In response to the challenges posed by overcapacity, China is increasingly emphasizing quality, innovation, and efficiency as drivers of economic growth and competitiveness. The government has rolled out initiatives to upgrade industries, promote technological innovation, and foster a transition towards higher value-added production. By shifting focus from quantity to quality, China aims to address overcapacity while fostering sustainable, innovation-driven growth.
Conclusion:
China’s overcapacity presents a complex and multifaceted challenge with profound implications for domestic and global economies. As China grapples with excess production capacity, policymakers, businesses, and stakeholders must collaborate to find sustainable solutions that balance economic imperatives with environmental, social, and geopolitical considerations. By addressing the root causes of overcapacity, fostering innovation, and promoting market-oriented reforms, China can mitigate the negative impacts of excess capacity while charting a path towards sustainable and inclusive economic development.
Connect with Factoring Specialist, Chris Lehnes on LinkedIn
Read more articles about the economy